Cracking the code of electric steam cracking
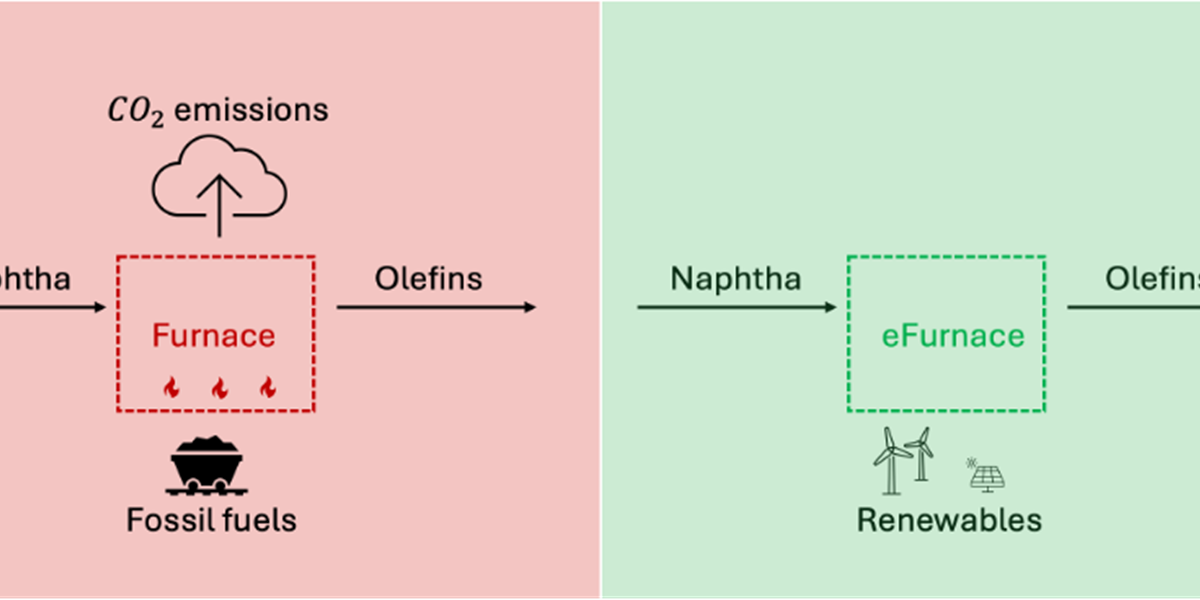
Modern economies are enabled by the industrial production of essentials materials, a process that is often accompanied by substantial carbon dioxide emissions. In 2020, the industrial sector was responsible for 36% of global final energy consumption, with the majority of this energy derived from fossil fuels. Consequently, the industry is accountable for one-fourth of global energy-related emissions, positioning it just behind the power sector as the top emitter. The stringent climate policies in Europe increasingly challenge the industry, making it difficult for investments to flourish without considering relocation. Therefore, innovation in industrial production is critical not only for the climate transition but also for the sustainability of Europe's economy.
The International Renewable Energy Agency (IRENA) suggests five pillars to reduce industrial emissions:
- Reduced energy demand
- Improved energy efficiency
- Improved material efficiency
- Circular economy practices
- Structural changes
The final pillar, structural changes, encompasses the adoption of clean energy and renewable heat sources, among others. This has a profound impact on the entire supply chain of material production as it directly affects the production process itself.
An illustrative example of how innovation facilitates structural change can be observed in petrochemistry. This sector ranks among the largest industrial polluters due to its production processes. Lighter alkenes, also known as olefins, are produced through a process called steam cracking. In this process, a hydrocarbon feedstock such as naphtha, LPG, or ethane is mixed with steam and briefly heated in a furnace at 850°C, without the presence of oxygen. The olefins generated are subsequently used in the manufacture of plastics and industrial solvents. However, this method is associated with significant emissions: for every metric ton of ethylene produced, 1 to 1.6 metric tons of are emitted. This results in annual emissions exceeding 300 million metric tons of , 70% to 90% of which can be attributed to the combustion of fossil fuels. The amount is comparable to the annual emissions of France in 2022.
This initiative led Shell and Dow to collaborate on establishing a startup for an experimental e-cracking furnace unit, situated at the Energy Transition Campus in Amsterdam. The e-cracking furnace introduces a method to heat steam electrically, aiming to decarbonize the entire cracking process. It is projected that 90% of scope 1 emissions could be reduced at costs that are economically competitive with traditional cracking methods. The experimental unit will serve to validate a theoretical model for electrifying current gas-fired steam cracker furnaces, facilitating quicker commercial-scale deployment. The next step involves designing and constructing a multi-megawatt pilot plant, which is slated to become operational in 2025. The Dutch government has shown support for this initiative by granting €3.5 million in funding, underscoring their confidence in the project's potential.
Figure: Difference between a regular steam cracking furnace and an eFurnace (Source: Econopolis Strategy)
The e-cracking furnace represents just one of numerous innovations aimed at facilitating the climate transition within the industrial sector. Other promising developments include steel production via electrolysis and solar-powered clinker production. Reimagining the industrial landscape is essential not only for combating climate change but also for retaining the industrial base within Europe. Moreover, such innovations are critical to enhancing the resilience of the European economy, ensuring its competitiveness and sustainability in the long term.